
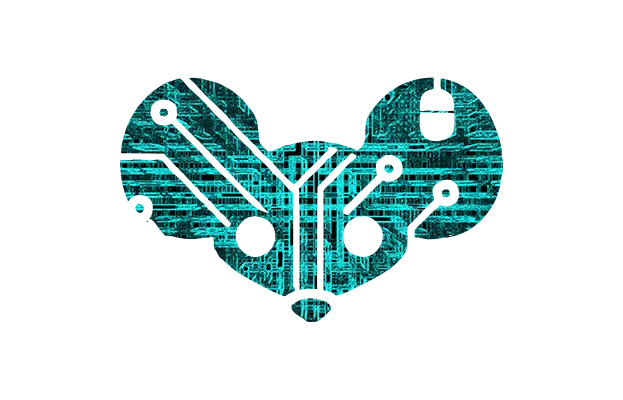
They mention standardisations and cost savings in their paper, as well as solving the heat load per cell problem by decreasing cell size. They also mention that there’s been a lot of micro-CPV module designs but that they haven’t been scaled up. Some quotes below:
Various researchers and developers have been exploring different micro-CPV module designs [5], [6], [7], [8], [9], [10], [11], [12], [13]. Most approaches have been tested on small prototypes or minimodules, while fewer have been realized with aperture areas (Aap) above 200 and 800 cm2,[…]
By decreasing the sizes of the primary optics and the solar cells, the heat load per cell is minimized. This reduction allows for sufficient heat spreading via the circuit board, enabling the direct assembly of solar cells onto the circuit board on glass.
At Fraunhofer ISE, we have developed a micro-CPV module concept [17], [18], [19], [20], [21], which is based on parallelized manufacturing processes and commercially available components.
The final module features a panel size of 24” × 18”, which is a standard in the microelectronics industry, facilitating machine adaption without necessitating special adjustments.
With the new sustainability laws in EU they have to offer 5 years of updates from the sale of their last unit.
https://single-market-economy.ec.europa.eu/news/new-eu-rules-durable-energy-efficient-and-repairable-smartphones-and-tablets-start-applying-2025-06-20_en